Home > Technical Support > Molding Technology > Molding Technology for DURAFIDE(R) PPS
5. Mold Shrinkage and Dimensional Accuracy
5.1 Mold Shrinkage
Reinforced DURAFIDE® grades have an extremely low mold shrinkage rate among the DURAFIDE grades; therefore, DURAFIDE is a quite suitable material for precision molding. |
(1) Molding on a side-gated mold
In Figs. 5-1, 5-2 and Table 5-1 are shown the mold shrinkage rates of typical grades of DURAFIDE. |
Test piece
Gate size
Cylinder temp.
Mold temp
|
: 80 × 80mm,
flat plate
: 4W × 2t
: 320°C
: 150°C
|
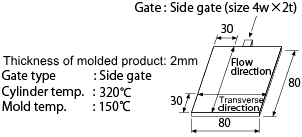
|
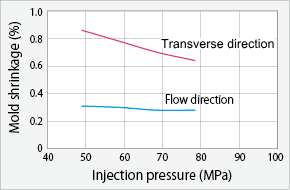 |
|
|
(b) 6165A4 |
Fig. 5-1 Mold Shrinkage of DURAFIDE® (Side gate)
|
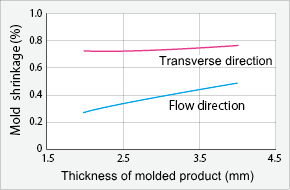 |
|
Fig. 5-2 Mold Shrinkage of DURAFIDE® 1140A1(Effects of thickness)
|
Table 5-1 Mold Shrinkage of DURAFIDE® |
Grade |
Mold shrinkage (%) |
Grade |
Mold shrinkage (%) |
Flow dir. |
Trav. dir. |
Flow dir. |
Trav. dir. |
0220A9 |
1.3 |
1.4 |
6150T6 |
0.2 |
0.6 |
1130A1 |
0.3 |
0.7 |
6165A4 |
0.3 |
0.6 |
1130A64 |
0.4 |
0.7 |
6165A6 |
0.2 |
0.5 |
1130T6 |
0.3 |
0.7 |
6165A7 |
0.3 |
0.6 |
1140A1 |
0.3 |
0.8 |
6465A62 |
0.3 |
0.7 |
1140A6 |
0.3 |
0.6 |
6565A6 |
0.3 |
0.4 |
1140A64 |
0.3 |
|
6565A7 |
0.3 |
0.5 |
1140A66 |
0.3 |
0.6 |
3130A1 |
0.4 |
1.0 |
1140A7 |
0.3 |
0.6 |
6345A4 |
0.3 |
0.7 |
1150A64 |
0.3 |
0.6 |
7140A4 |
0.1 |
0.5 |
2130A1 |
0.1 |
0.6 |
7340A4 |
0.3 |
0.5 |
Molded product
Gate
Cylinder temp.
Injection pressure
Mold temp.
|
: 80 × 80 × 2mmt, flat plate
: Side gate (size 4w × 2t)
: 320°C
: 60MPa
: 150°C (100°C for 6565A6 and 6565A7) |
* Values shown here are typical values, and when making a mold, they must be adjusted according to the wall thickness, gate size and molding conditions. |
(2) Molding on a Pin-point gated Mold
Mold shrinkage rates of DURAFIDE 1140A1 and 6165A4 are shown in Fig. 5-3. The mold shrinkage rate of a flat plate molded on a pin-point gated mold will be the mean value of the shrinkage rates in the flow direction and transverse direction of a part molded on a side gated mold.
|
Test piece
Gate position
Cylinder tem
Mold temp |
: 50 × 50mm, flat plate
: One point at center
: 320°C
: 150°C |
|
|
(a) 1140A1 |
(b) 6165A4 |
Fig. 5-3 Mold Shrinkage of DURAFIDE® (Pin-point gate)
|
5.2 After Shrinkage
The purposes of annealing are (1) elimination of residual strain, and (2) dimensional stabilization. In the case of (1) elimination of residual strain, annealing for 1 hr. at a temperature slightly above the glass transition point Tg (100°C to 120°C) is effective. In the case of (2) dimensional stabilization, if the ambient temperature is higher than mold temperature, the after shrinkage must be completed to avoid dimensional changes in the ambient temperature. If the highest service temperature is 160°C, it becomes necessary to anneal at a temperature about 20°C higher; i.e., 180°C.
Fig. 5-4 shows the after-shrinkage rates of DURAFIDE test pieces, molded at a mold temperature of 150°C and treated at respective annealing temperatures. |
|
|
(a) 1140A1 |
(b) 6165A4 |
|
Fig. 5-4 After Shrinkage of DURAFIDE®
|
5.3 Dimensional Accuracy
Dimensional accuracy of 6165A4 is shown in Table 5-2.
Looking at the coefficients of variation, dimensional fluctuations of 6165A4 on molding are as small as 0.027% in a single day and 0.030% during the day in a year. So it is possible to obtain molded products of high dimensional accuracy. |
|
Table 5-2 Dimensional Accuracy of DURAFIDE® 6165A4 |
Data tested |

(mm)
|

(mm)
|
|

in three days
continually
|
|
88.08.10 |
49.766 |
0.004 |
0.0024 |
0.024 |
Fluctuation over a year
49.766
±0.015
 0.030(%) |
11 |
49.766 |
0.003 |
0.017 |
12 |
49.769 |
0.004 |
0.025 |
88.11.71 |
49.769 |
0.004 |
0.026 |
0.028 |
18 |
49.766 |
0.004 |
0.025 |
19 |
49.765 |
0.004 |
0.025 |
89.02.27 |
49.765 |
0.006 |
0.036 |
0.036 |
28 |
49.762 |
0.007 |
0.043 |
29 |
49.763 |
0.004 |
0.026 |
89.05.29 |
49.766 |
0.005 |
0.029 |
0.027 |
30 |
49.767 |
0.004 |
0.022 |
31 |
49.768 |
0.005 |
0.029 |
Average daily
fluctuation
|
|
|
0.027 |
|
|
|
|
Test piece : 50 × 50 × 3t, pin-point gate. |
|