HOME > 製品情報 > DURAFIDE(R) PPS
無理抜き成形を実現する ジュラファイド(R) PPS
はじめに |
従来、自動車における冷却系部品(冷却水制御バルブ、インレット、アウトレットパイプなど)は6-6ポリアミドや芳香族ポリアミドが主に使用されてきました。しかし、これらポリアミドは加水分解による強度低下や吸水による寸法変化などを起こすため、設計者にとっては使用が難しい材料です。一方、冷却系部品においてPPSが採用される事例が昨今非常に増加しています。PPS(ポリフェニレンサルファイド)には、連続使用温度200~240℃で示される高い耐熱性に加え、200℃以下で溶解する有機溶媒がない等、フッ素樹脂に匹敵する耐薬品性があり、ポリアミドのような加水分解、吸水による寸法変化もほとんど起こしません。このような長期信頼性の高さは製品設計におけるPPSの大きな魅力です。図1に冷却系部品の一例を示します。
通常、冷却系部品とゴムホースの連結部分はバルジ形状となっているため、金型設計にアンダーカット形状が発生します。金型からの離形をスライド構造にするとパーティングライン(金型の合わせ目)にバリが生じます。しかし、この連結部分(ポート部分)のバリは、気密漏れ、ゴムホースへのダメージの懸念から、一般的に許容されていません。そのため、成形品のバリ取りを行うか、ポリアミド系の材料では無理抜き成形が既に実施されています(無理抜き成形の説明は後述)。一方で、PPSの場合、材料自体の脆さから無理抜き成形はこれまでほとんど行われておらず、基本的にはバリ取りを行っており、コストアップの一因となっています。
そこで、今回PPSの無理抜き性の確認を行うと共に、ジュラファイド® PPSの無理抜き成形が可能なグレードを紹介します。 |
1. 無理抜き成形とは |
製品にアンダーカットがあっても、スライド構造を使用せず、二方向に“無理”に製品を変形させて金型から離型することを無理抜き成形といいます。パーティングライン(金型の合わせ目)がなくなるため、バリレス成形が可能で、バリ取り工程を削減することでコストダウンができます。図2に無理抜き成形の工程例を示します。キャビティに樹脂を充てん後、コアを先に抜き(型開1)、製品が内側に変形できる状態にした後に外側の金型を開き(型開2:この時点で無理抜きが行われます)、最後に製品を離型して完了です。ポート部には金型の合わせ面がありませんので、バリができません。 |
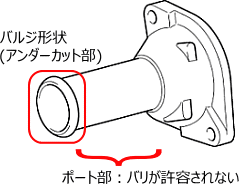 |
図1:冷却系部品例(インレットパイプ) |
|
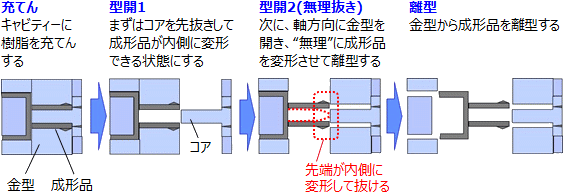 |
図2:無理抜き成形工程例 |
ここから先は、オンラインテクニカルサポート「WEB@TSC」の会員の方
(登録は無料)のみご利用いただけます。ログインしてご覧ください。 |
 |
 |
|